Positioned before the filling machine, the deaeration unit creates a vacuum inside each bottle and injects inert gas to void the space of any harmful particulates and oxygen, which allows the bottle to arrive at the filling stage saturated with the inert gas, having the risk of oxidation drastically reduced (up to 90% less oxygen). To ensure an ease of use, SRAML bottle de-aeration units come mounted on a height-adjustable platform to allow for the rapid transition between formats.
Bottle deaeration — inert gas injection unit
The bottle deaeration unit replaces air in an empty bottle with inert gas before the filling process. Vacuuming the bottle before the gas injection significantly improves the deaeration process. When filling deaerated bottles, the product is exposed to the inert gas only, reducing the oxygen absorption. The inert gas is evacuated from the bottle into the filler bowl where it is creating the same inert atmosphere. The system is not suitable for PET bottles since they can be deformed by strong vacuum. A bottle is placed under the deaerator for it to descend onto the bottle. A high-vacuum pump removes most of the air from the bottle to inject inert gas, typically nitrogen. The unit is equipped with “no bottle — no injection” system to stop the deaeration process if the bottle is not present.
Bottle inert gas injection unit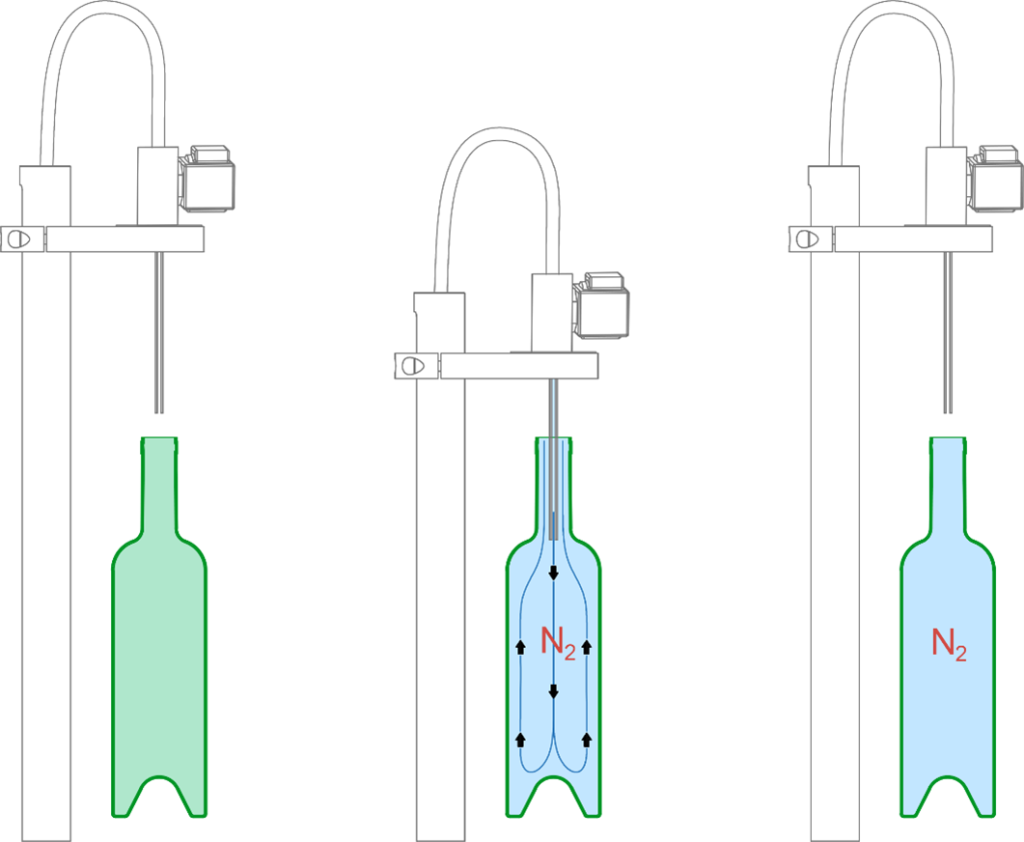
Bottle inert gas injection unit replaces the air in an empty bottle with inert gas before the filling process. When filling deaerated bottles, the product is exposed to inert gas only, reducing oxygen absorption. The inert gas is evacuated from the bottle into the filler bowl to create the same inert atmosphere. The bottle is placed under the inertization unit for it to descend onto the empty bottle and inject it with inert gas (typically nitrogen). Equipped with “no bottle — no injection” system, the deaeration process is only done when the bottle is present.